Play Movie
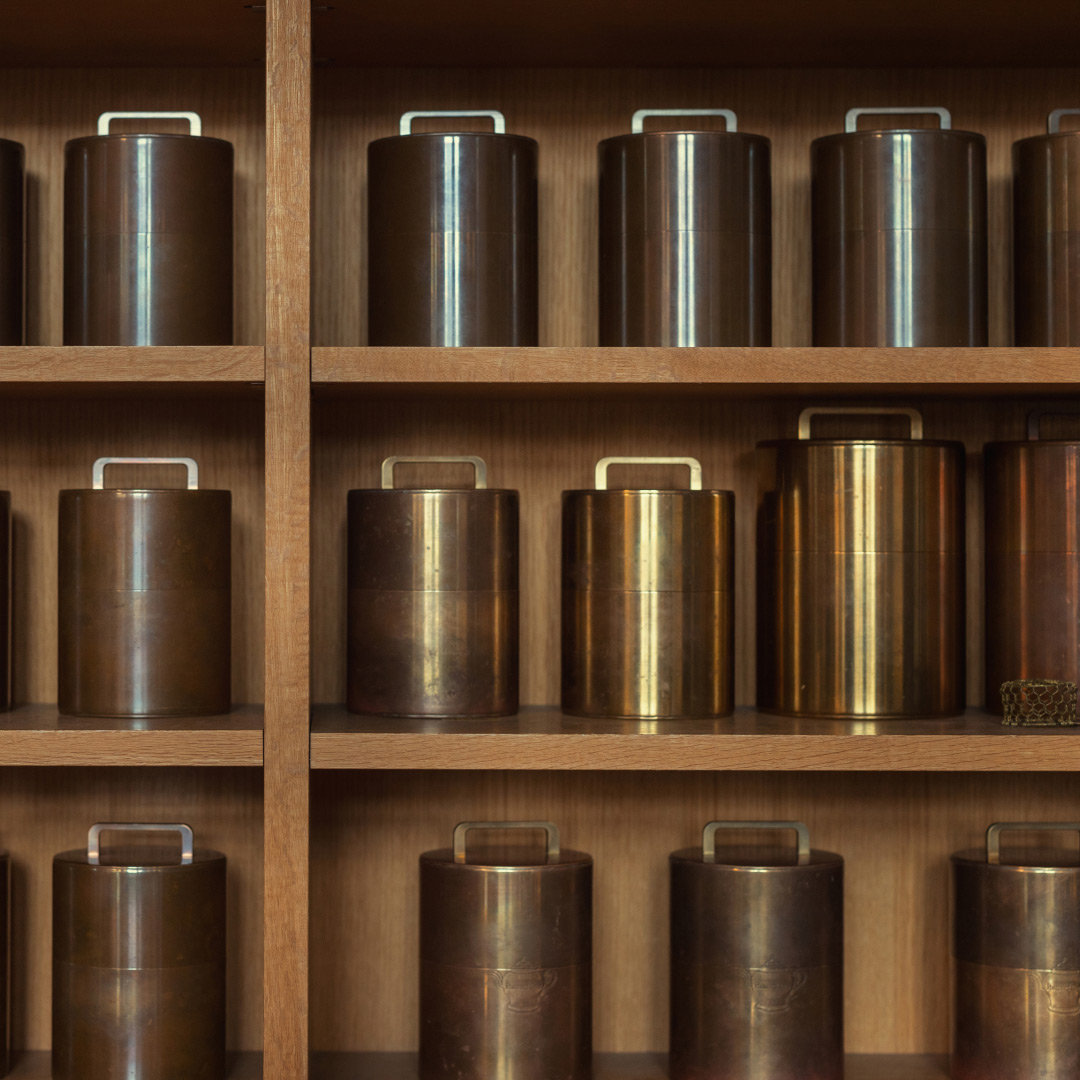
Listen
to Katherine Kennard
reading this story
Tea caddies lasting generations
Kaikado
In the simplest of terms, Kaikado’s signature tea caddies can be described as living tools. Cylindrical in shape, each chazutsu (‘cha’ means tea, ‘zutsu’ means canister) is the result of a century-old process that transforms metal sheets into lustrous containers over the course of more than 130 steps. Beyond their aesthetic proportions, there is an enduring functionality to the airtight canisters, protecting tea leaves and other food items from moisture and humidity. At the same time, they undergo a beautiful evolution through use, with the colours gradually maturing to reflect the passing of time.
Founded in Kyoto in 1875, Kaikado became known for producing metal canisters using imported tinplate from England. The Kaikado name is synonymous with high-quality canisters, which are still made by hand in the company’s workshops, following the same processes developed and passed down by its founder.
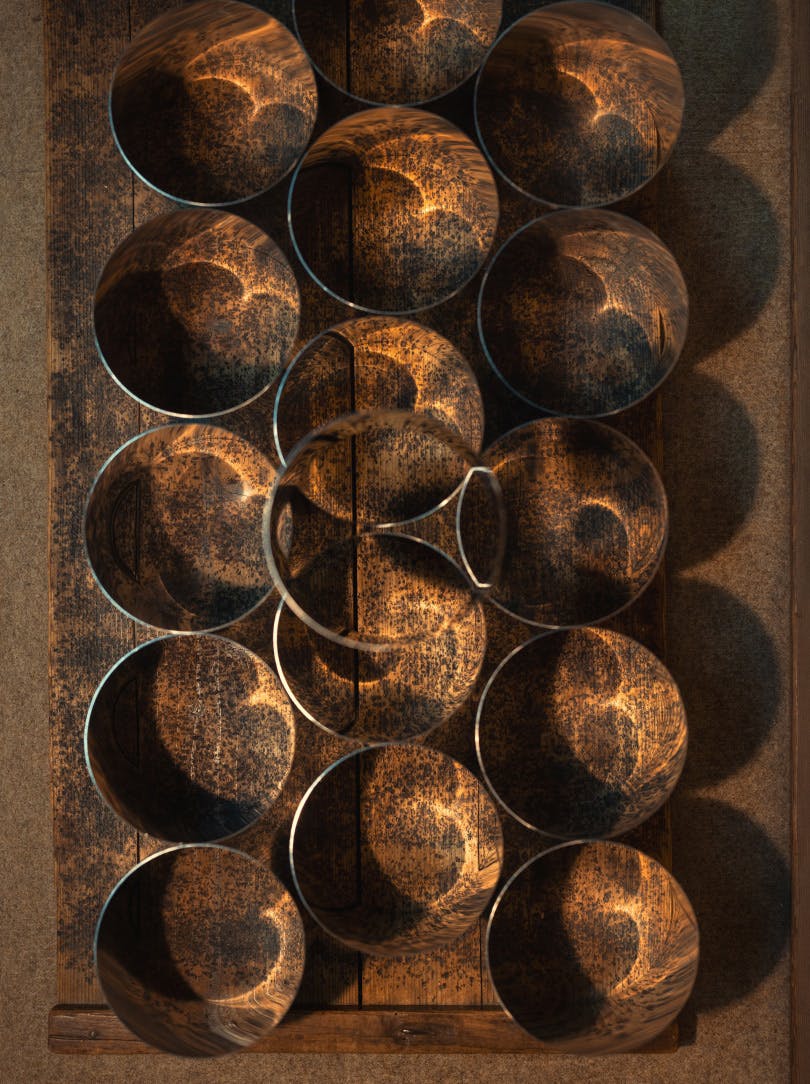
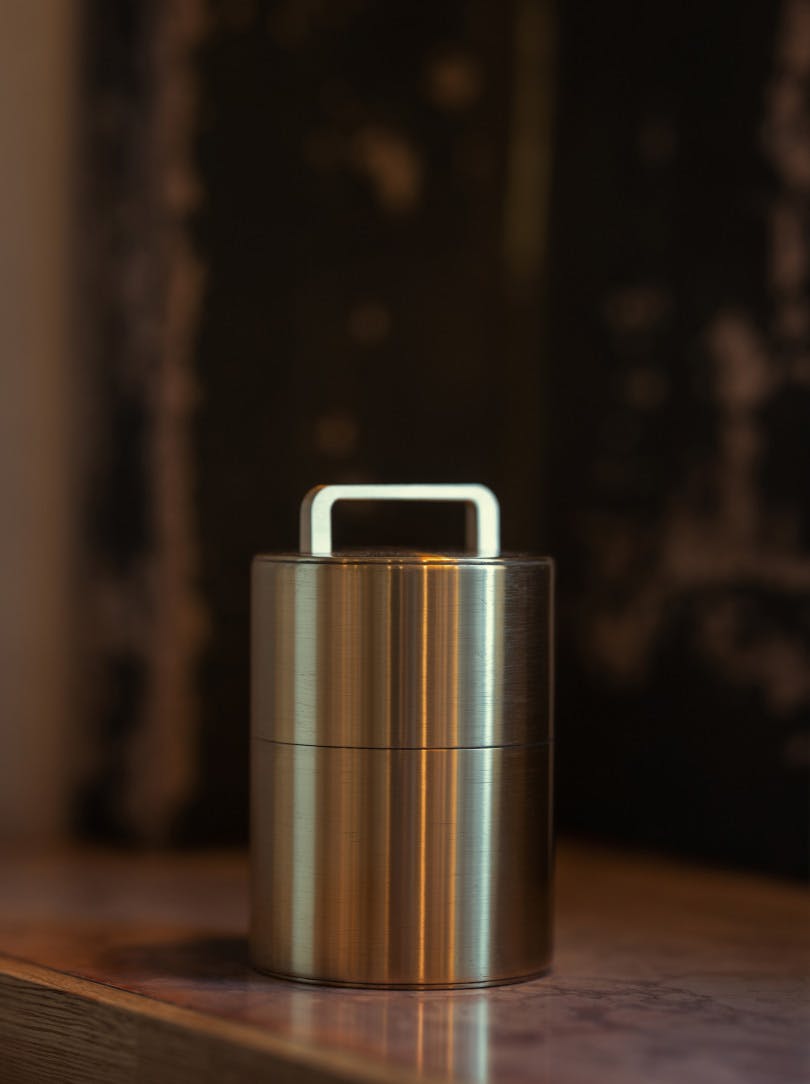
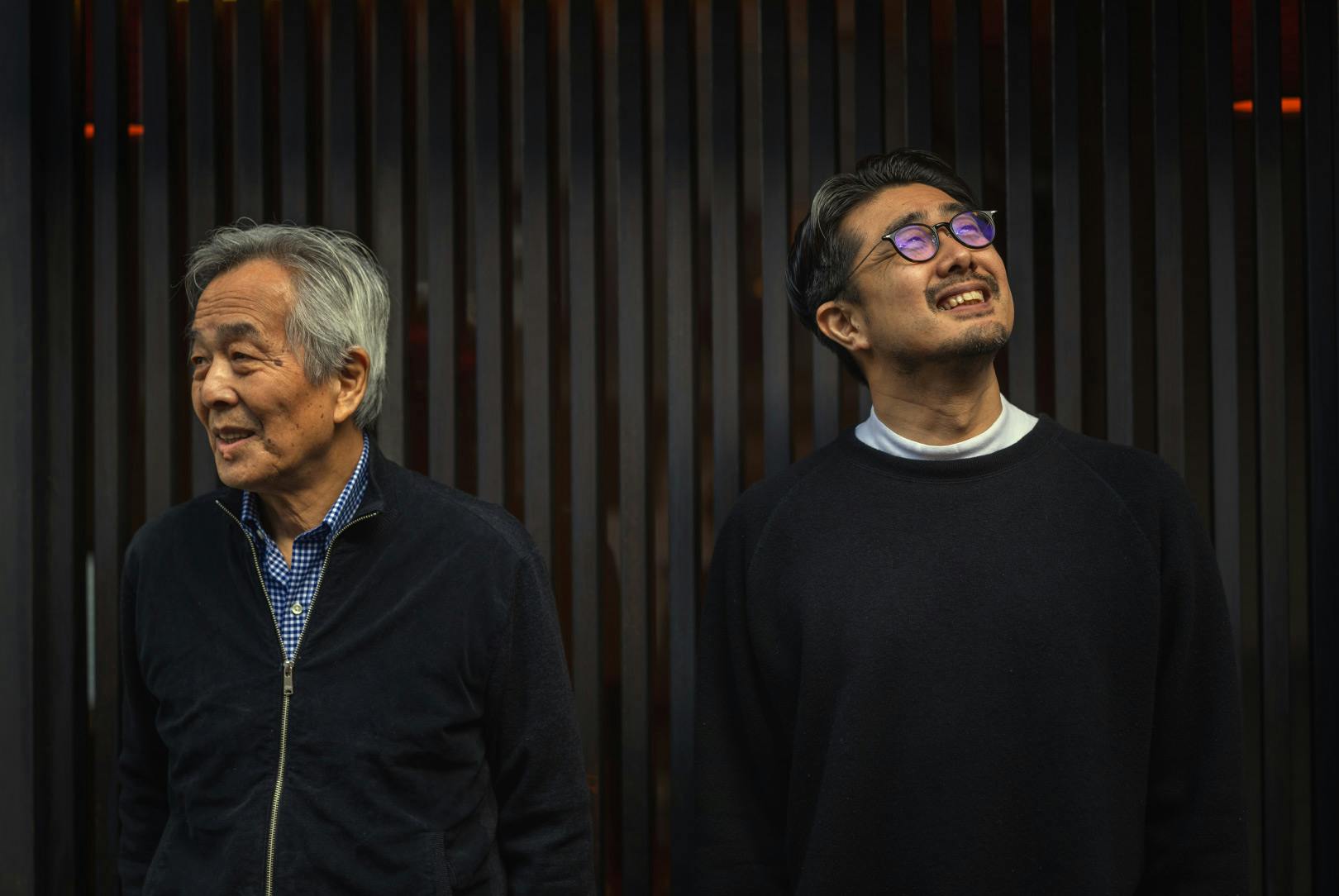
Today, Kaikado’s headquarters can still be found in Shimogyo ward, just a short stroll from Gojo Bridge and the Kamo River. There is an office and a small shop, its shelves lined with various canisters, along with two workshops, one of which has been operating for more than a century. It’s here that you’ll find a small team crafting items on a daily basis, joined by the company’s sixth-generation craftsman and managing director, Takahiro Yagi, and his father and company chairman, Seiji Yagi.
“I joined Kaikado straight out of school and have been here for almost 55 years,” explains Seiji. “I’m a fifth-generation craftsman and it was a natural progression to take over the company from my father. This is the only job I’ve ever known.”
Alongside Seiji is his son Takahiro, who began working for Kaikado in 2000 and later took over the role of managing director. Takahiro’s return to the family business was the result of a chance encounter that cast their products in a whole new light. While working at a souvenir shop, he encountered an American customer purchasing a tea canister. Upon enquiring about whom the gift was for, he was surprised to learn they planned to use it in their kitchen at home.
“American culture is so completely different to ours, so I figured that if Kaikado canisters could be used in America, they could be used anywhere,” he recalls. “I returned home and told my father that I wanted to come back and sell our products outside Japan. It’s not that simple, he replied. First of all, I had to learn how to make them.”
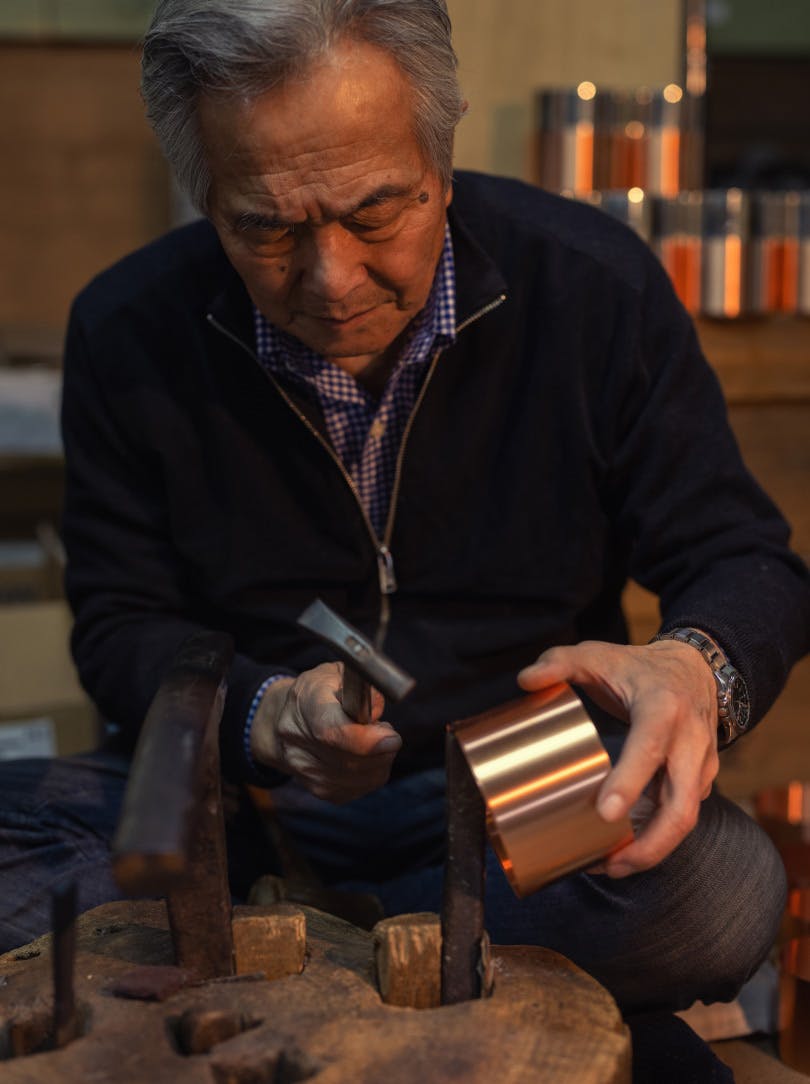
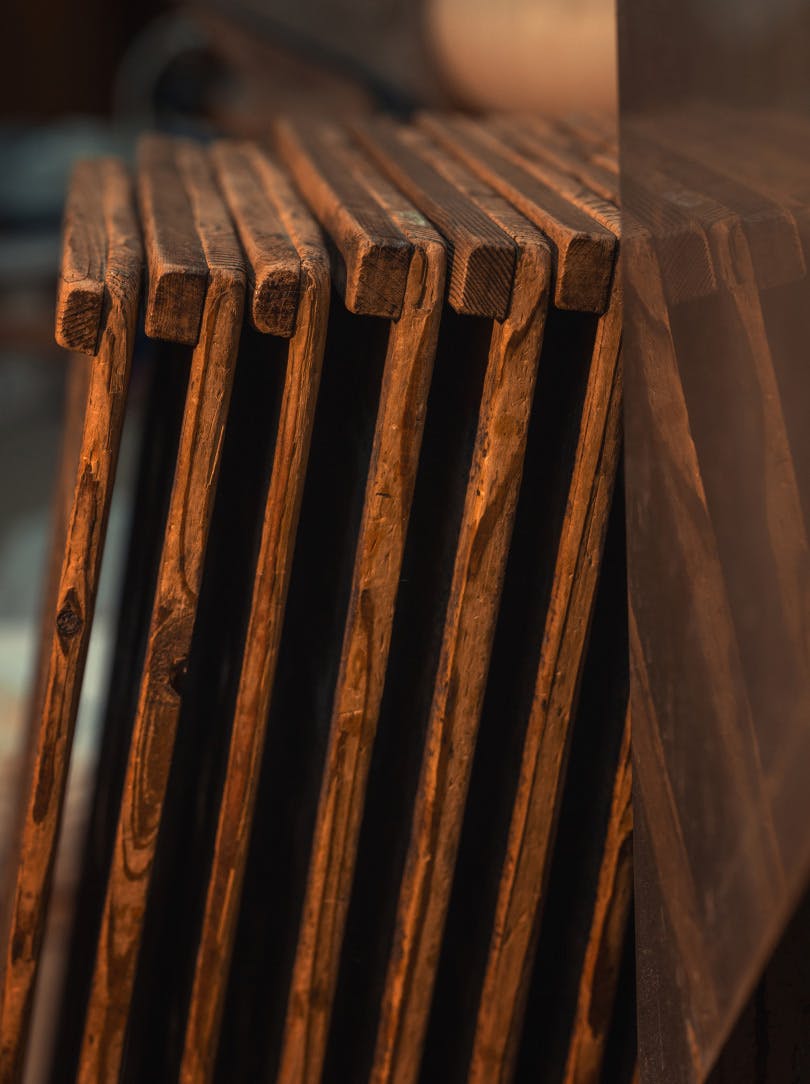
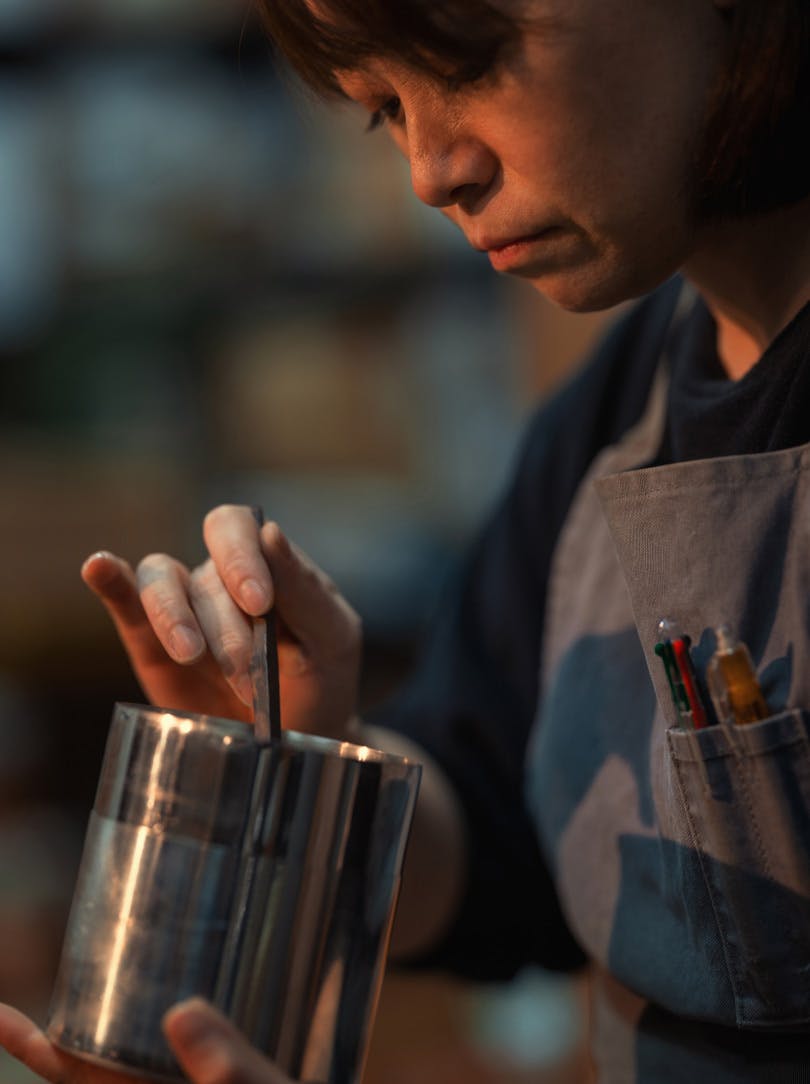
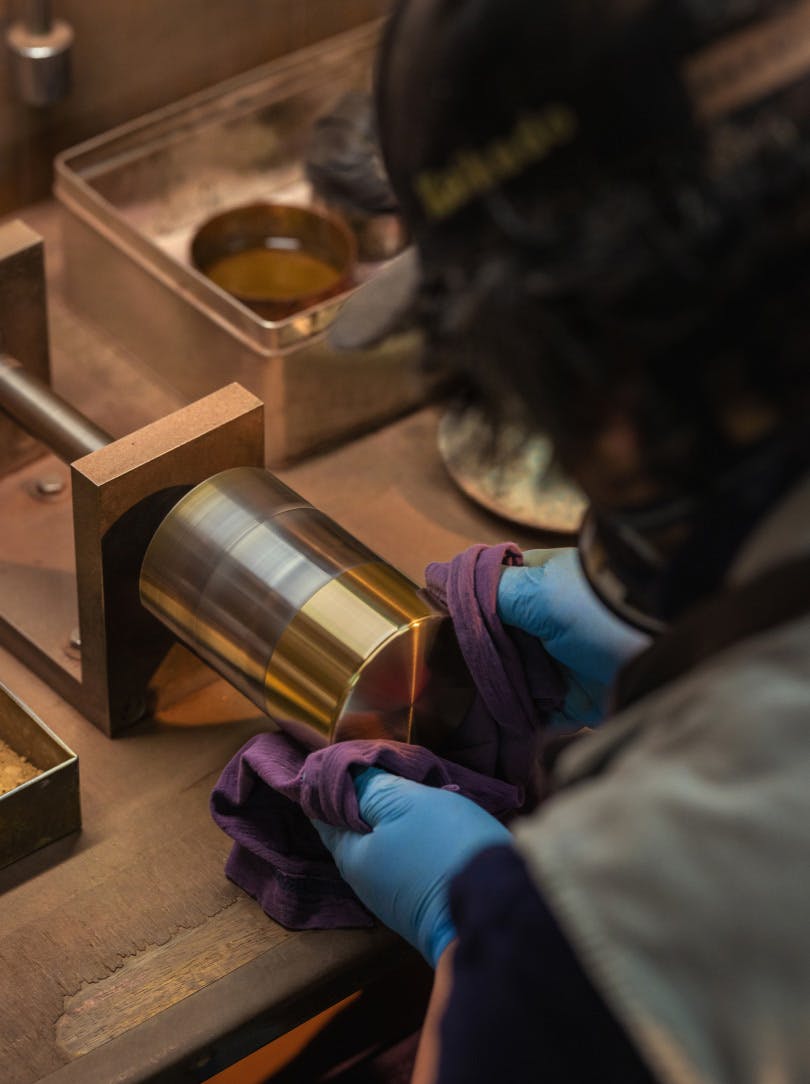
The process of making a Kaikado canister has remained unchanged for more than a century. Comprising more than 130 procedures, from cutting and shaping to soldering and polishing, the techniques and the knowledge behind them have been successfully passed down from each generation to the next. Drawing on his vast experience, Seiji remains the authority on making, a role that will eventually be handed to his son.
“There are over 130 steps, but you can’t simply remove one – each and every single step is important. Everything has a purpose, whether it’s making the chazutsu easier to use, more comfortable to hold or look more balanced,” explains Seiji. “My father never really taught me how to do things. I just had to watch, remember and then do it myself.”
Takahiro nods in agreement. “If someone tells you what to do, you only end up remembering the surface-level information. Everyone is different, so remembering the 130 steps is not important, what’s really important is what those 130 steps allow you to make. If you focus too much on the individual steps, you lose sight of the big picture. The products start to falter and eventually lose their essence.”
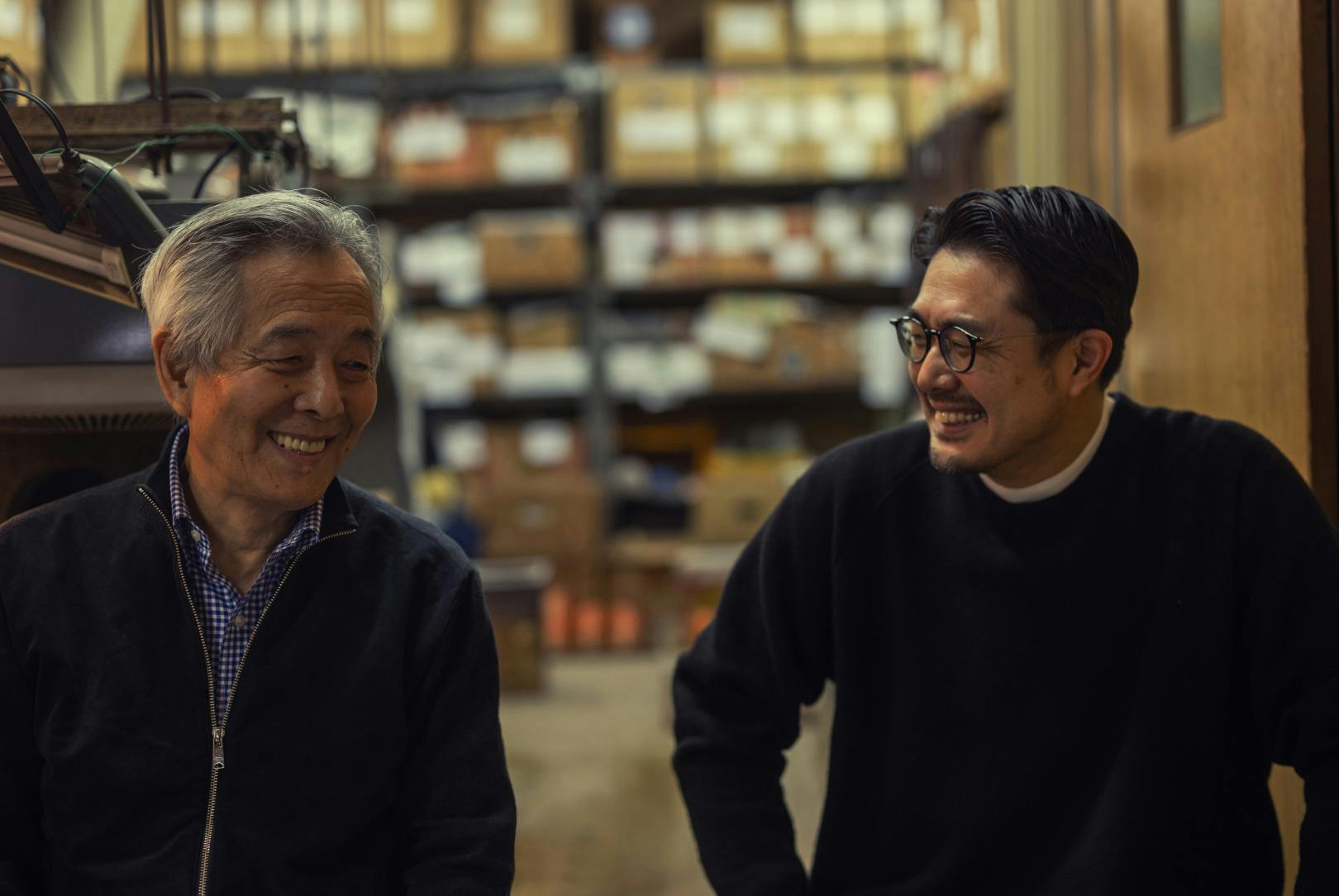
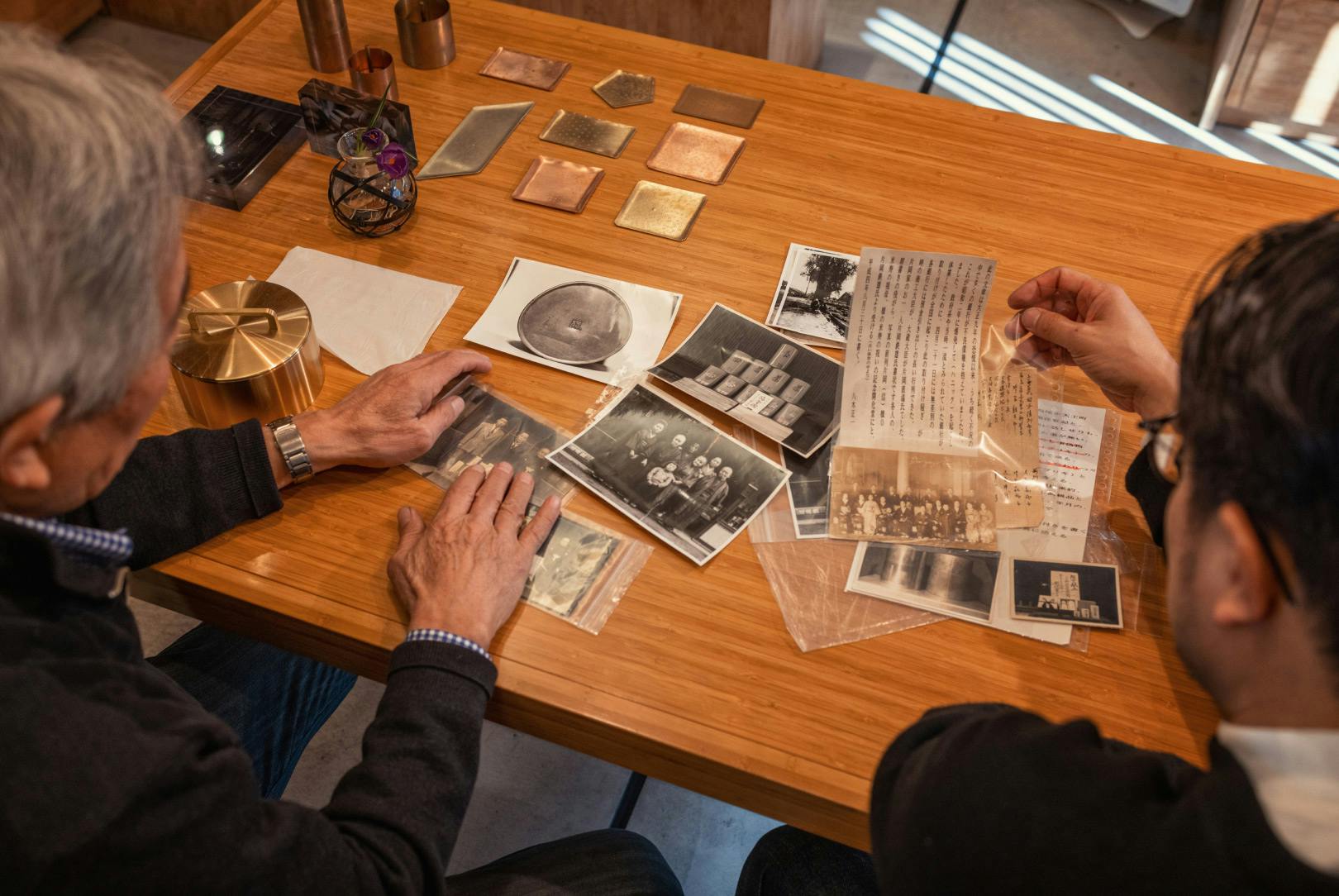
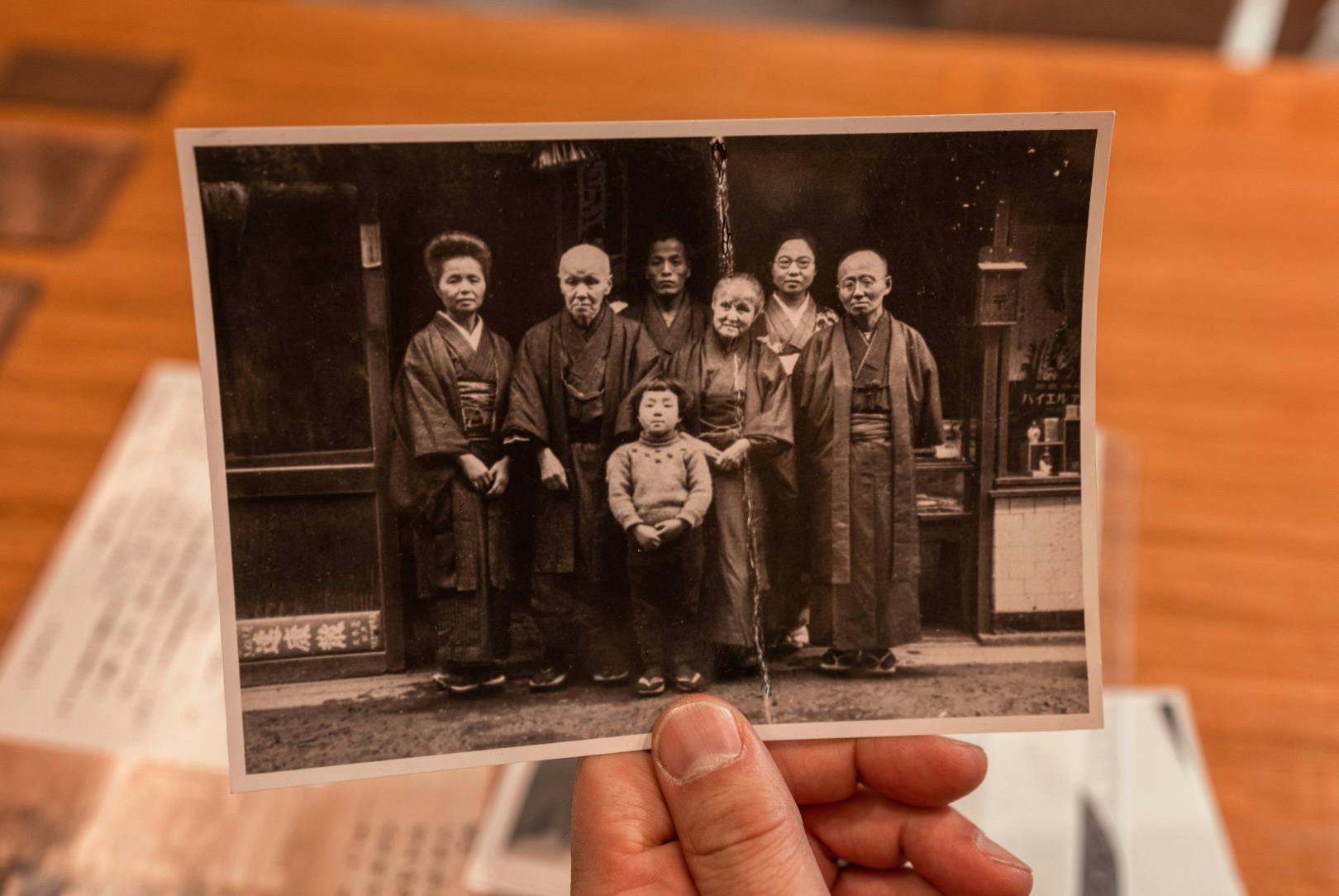
Just like the five generations of the family before him, Takahiro is, first and foremost, a craftsman. His hands-on knowledge of making, gained from countless hours spent in the workshop, provides the foundation for his work as Kaikado’s managing director. Since the company’s first overseas pop-up in 2005, he has introduced chazutsu to a global audience. At the same time, he explores the potential of craft in a changing world, be it through exhibitions, interactive experiences or cross-industry collaborations.
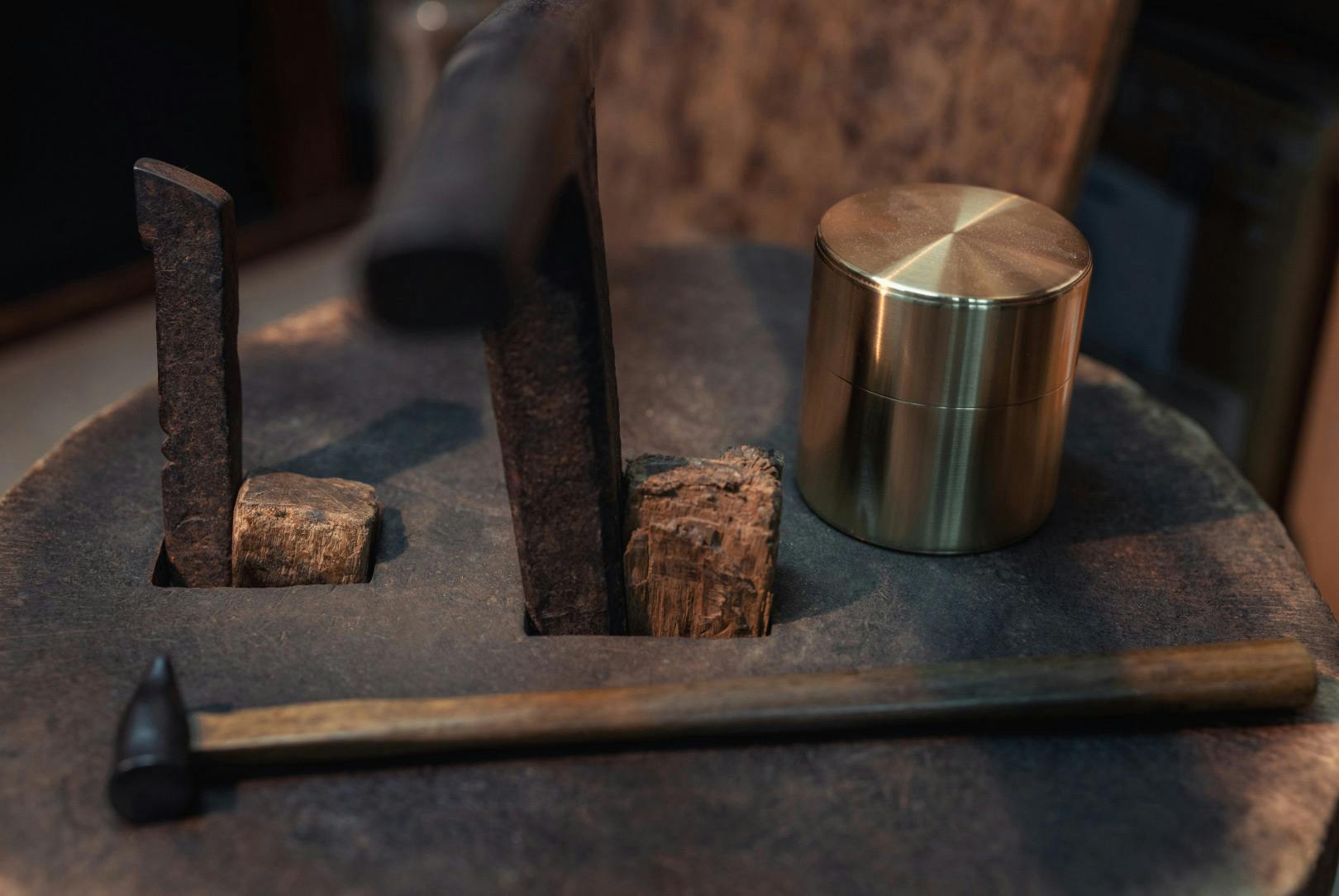
“In my grandfather’s era, machine-made products were considered good, while handmade products were too old-fashioned. It was really tough for him during that time,” says Takahiro. “I feel so grateful for this current era. People are taking a fresh look at handmade products, reconsidering their value.”
“Rather than just sitting back and taking it all in, this allows us to pursue things for the future. What can I start now for my children, and their children after that? I feel that now’s the time to consider those questions.”
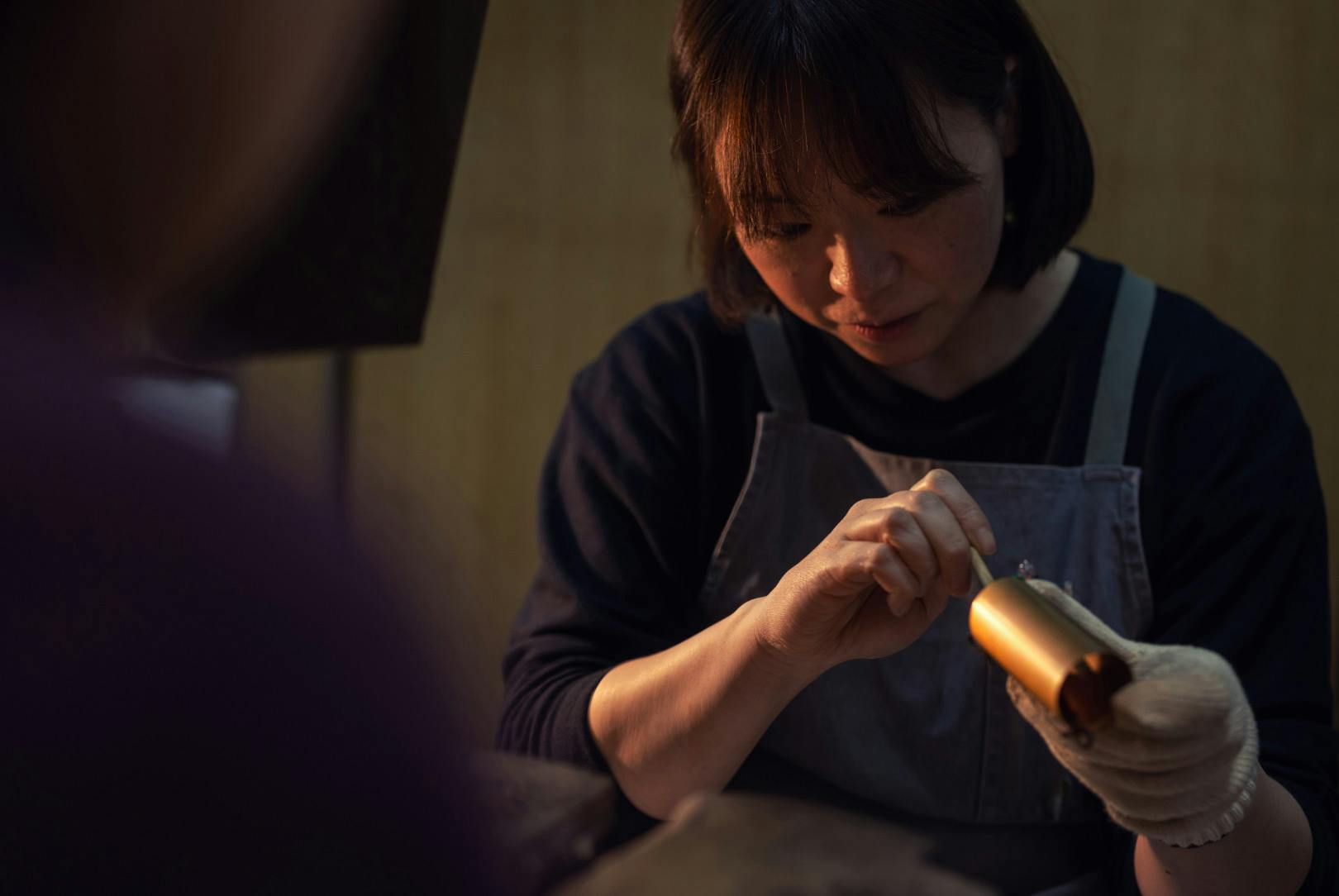
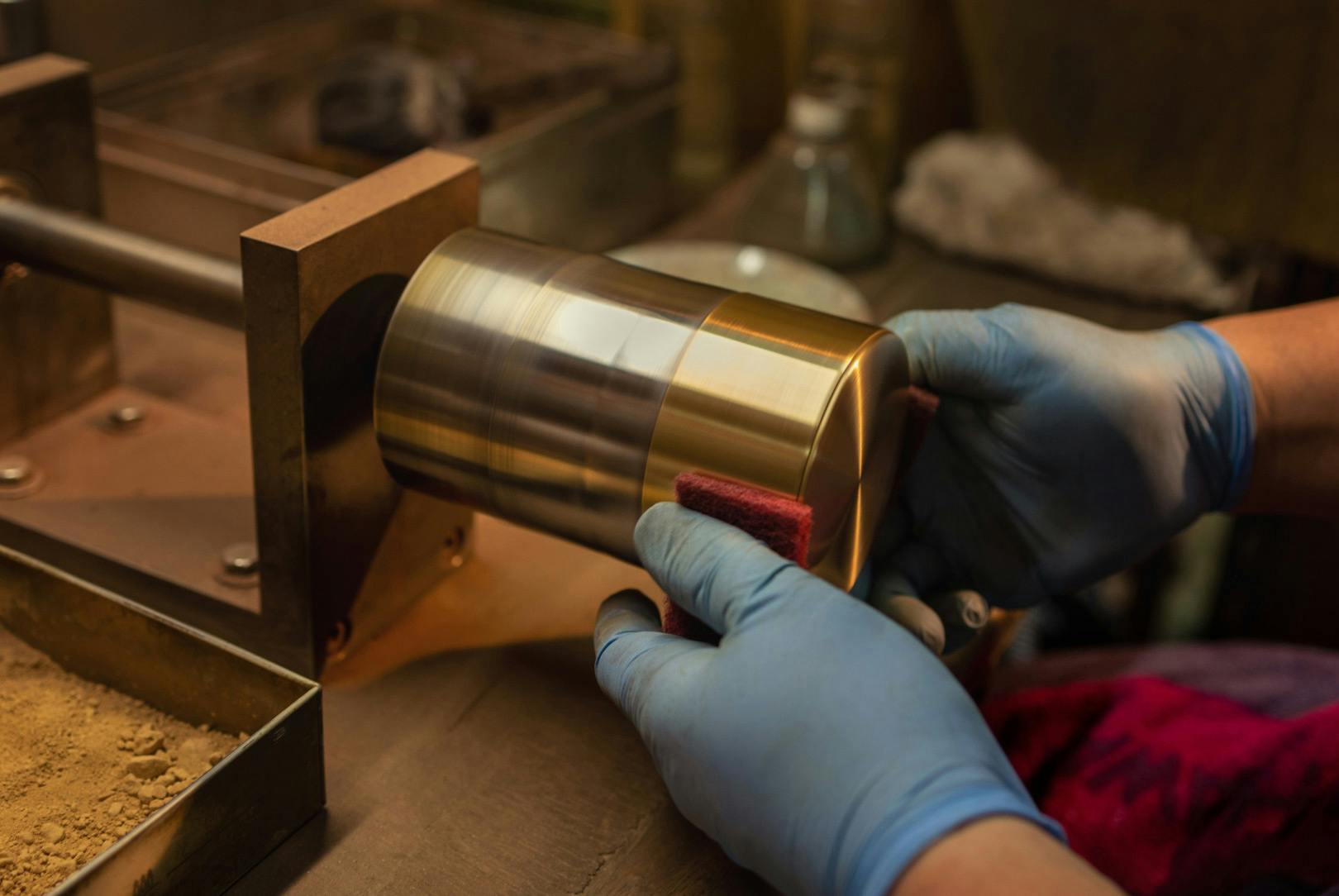
The endearing nature of Kaikado’s handmade canisters extends beyond the design itself. Upon closer inspection, the quality of craftsmanship is evident in the meticulous manufacturing and attention to detail. From the carefully soldered joints to the slightly rounded corners and ever-so-smooth connections, each and every detail has been carefully considered. However, the products also possess a sense of familiarity, a character that reflects the human touch.
“Tokyo is undoubtedly cool, but Kyoto is actually a bit rustic and people here prefer less flashy designs,” says Takahiro. “Something about our canisters is ever so slightly untrendy. I think that’s why people use them for such a long time. If a design is too trendy, people grow tired of it and eventually move onto the next big thing.”
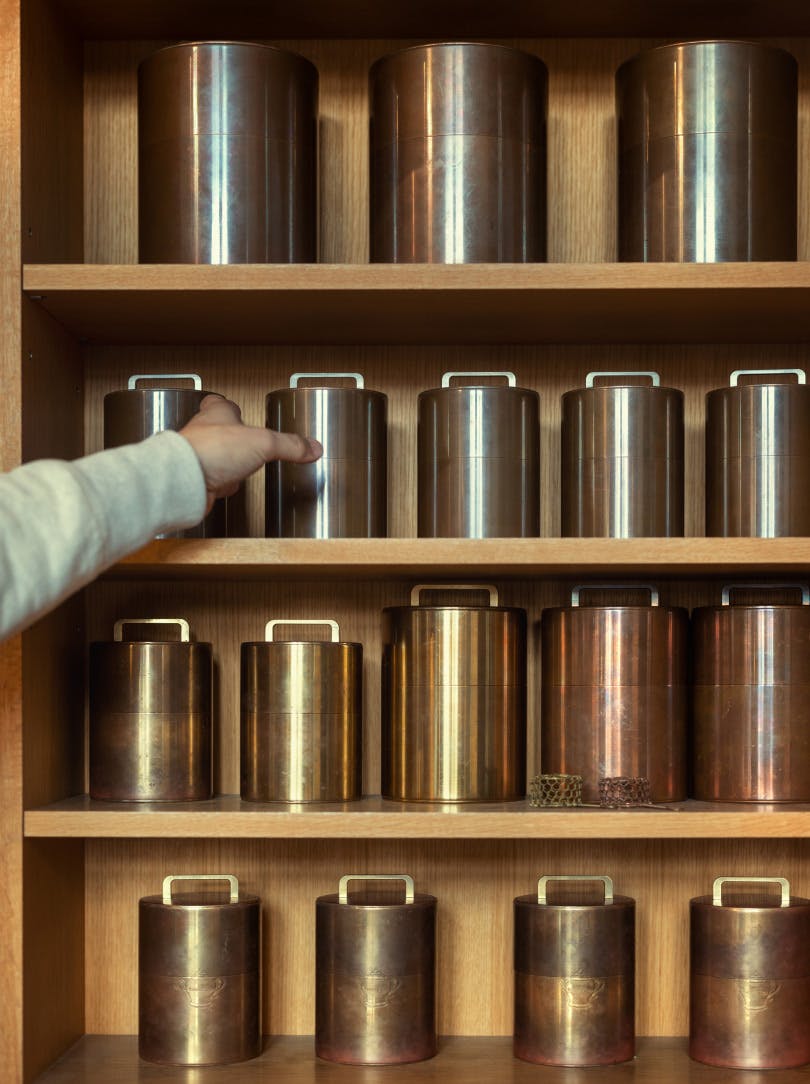
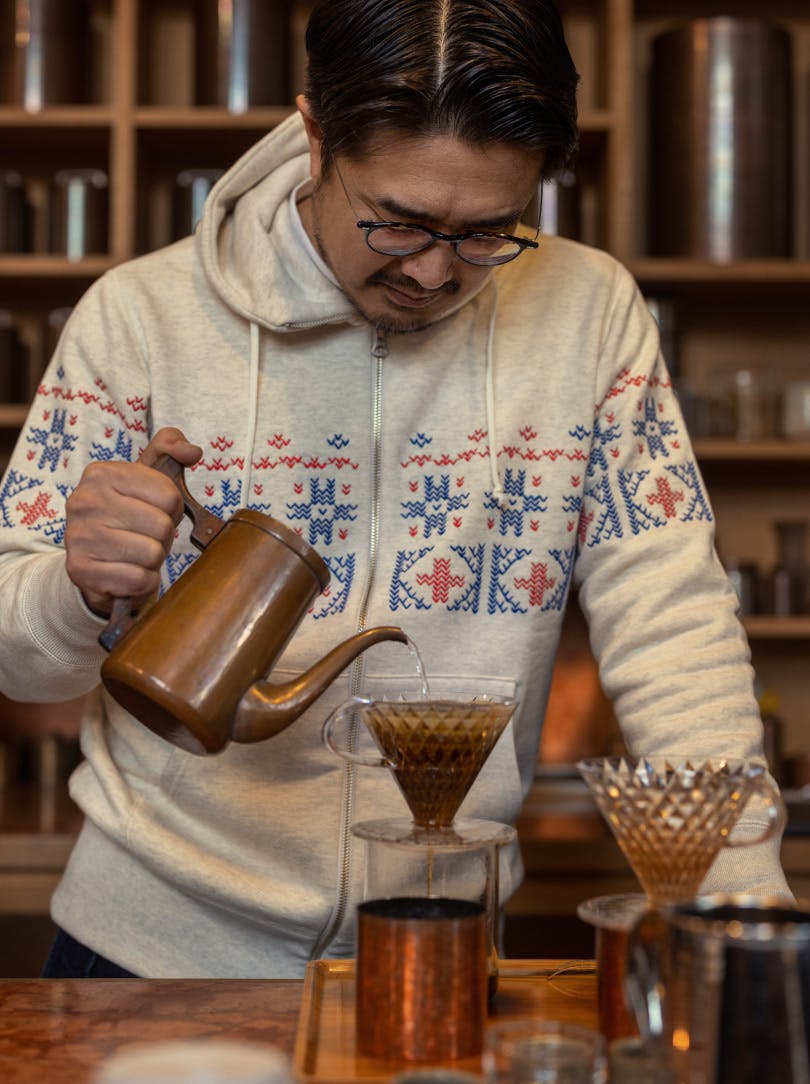
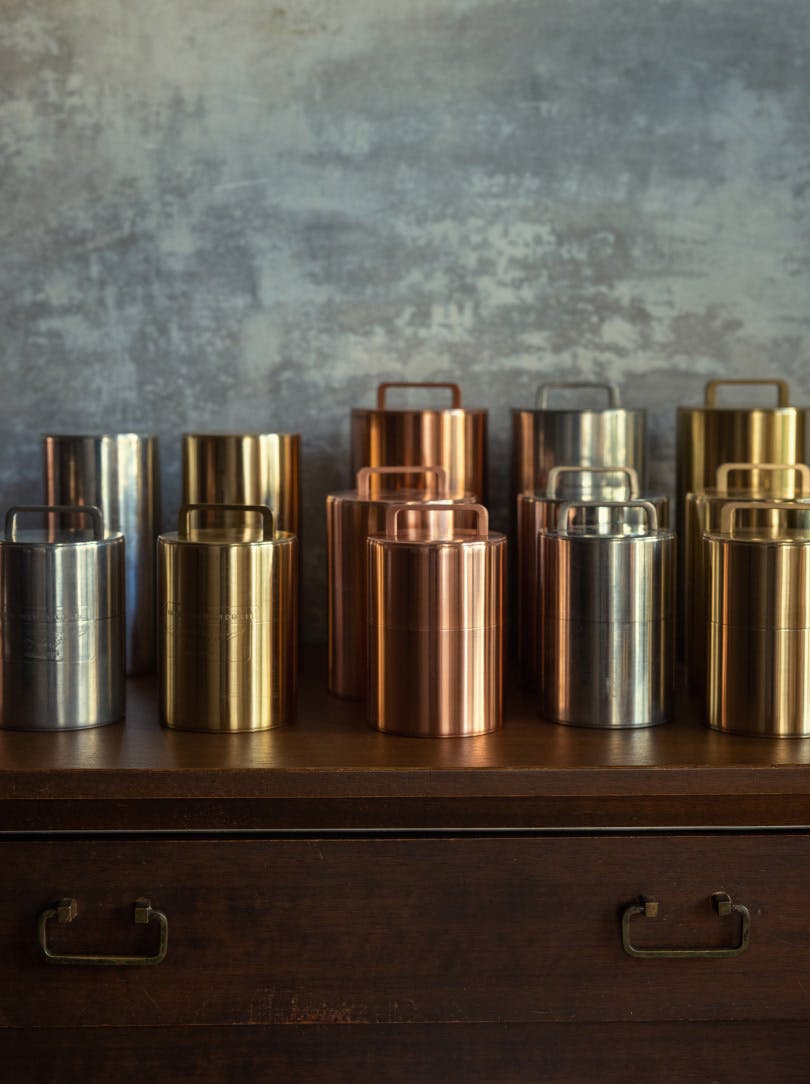
Venturing over to the adjacent workshop, the afternoon shift has begun. Workstations are spread throughout the elongated interior and multiple processes are happening in unison at any given time. Work proceeds with unspoken understanding, set against a backdrop of wheels whirring, hammers tapping and soldering irons singeing. The small team includes eight craftspeople, who produce around 40 to 50 units per day.
“In the workshop, different people complete different tasks. However, they all need to work with the same sensibility. It’s essential that Kaikado has a single, consistent character when making things. That’s the most challenging part. Defining that character and atmosphere is difficult, but Kaikado has a certain essence that everyone is focused on, which is why we are able to do what we do. In our morning meetings, we often talk about working and making things the Kaikado way, and I think that being able to maintain that essence has been key to our survival,” explains Takahiro.
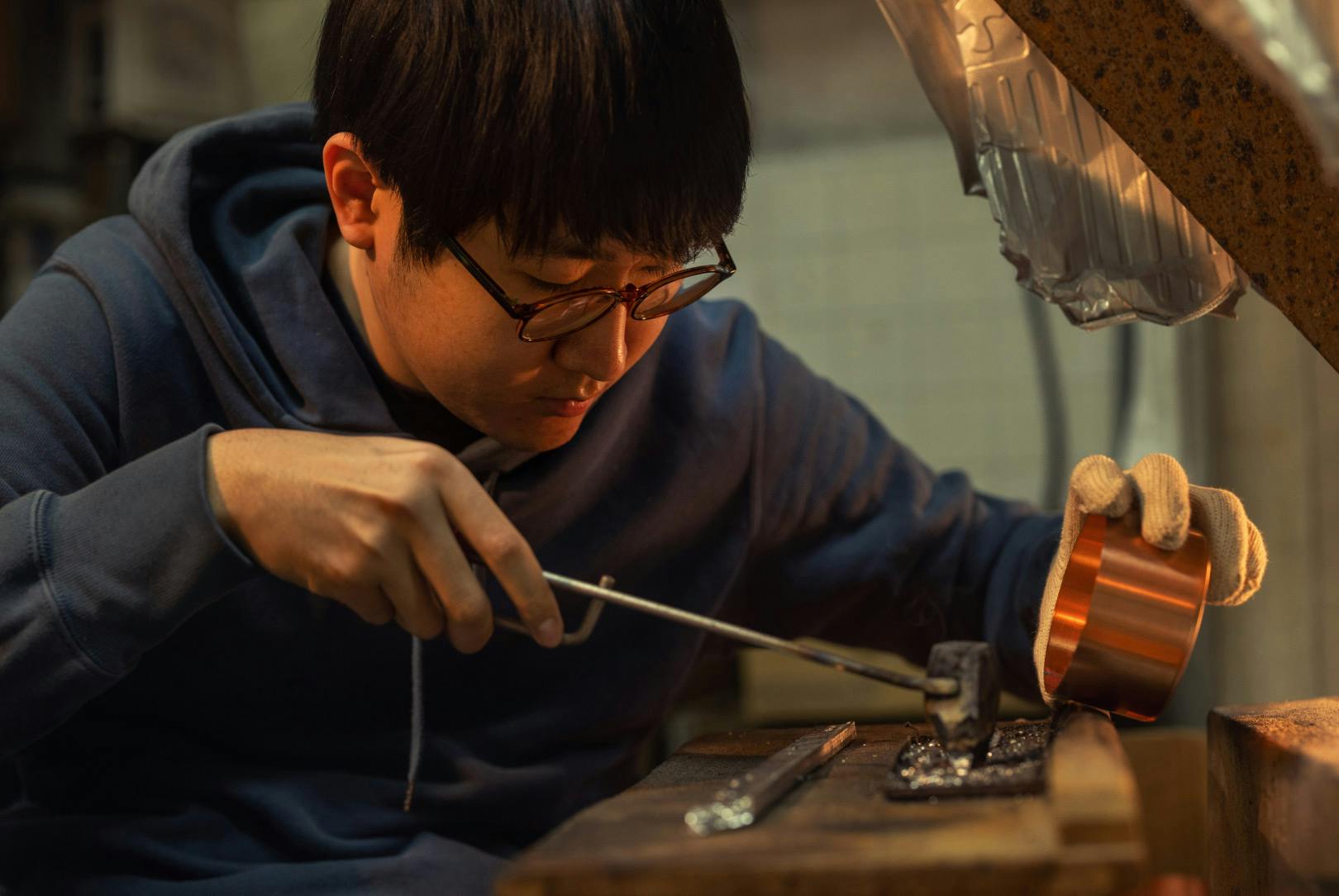
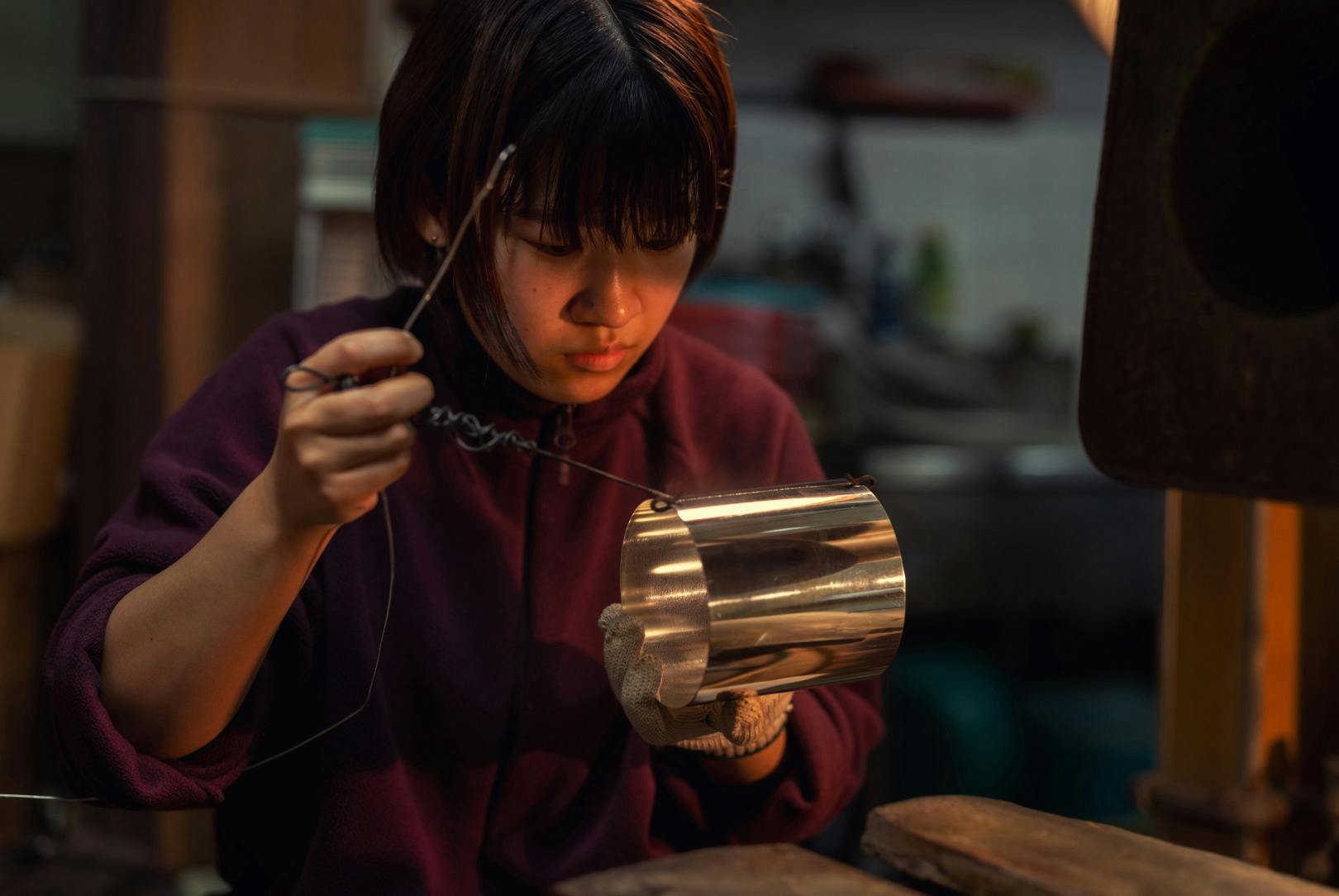
Operating at this scale, where employees are considered family, rather than seeking rapid growth has been crucial to overcoming the challenges that have arisen throughout the company’s history. The simple notion of continuing to make products on a daily basis, just as their predecessors did, is also central to their philosophy.
“Tradition means changing while also remaining the same. Some things have to stay, but changes are still required to bring us into line with the current era. If Kaikado changes too much it will lose its essence, which is why we continue to change yet stay the same. The most important thing is that we keep making tea canisters.”
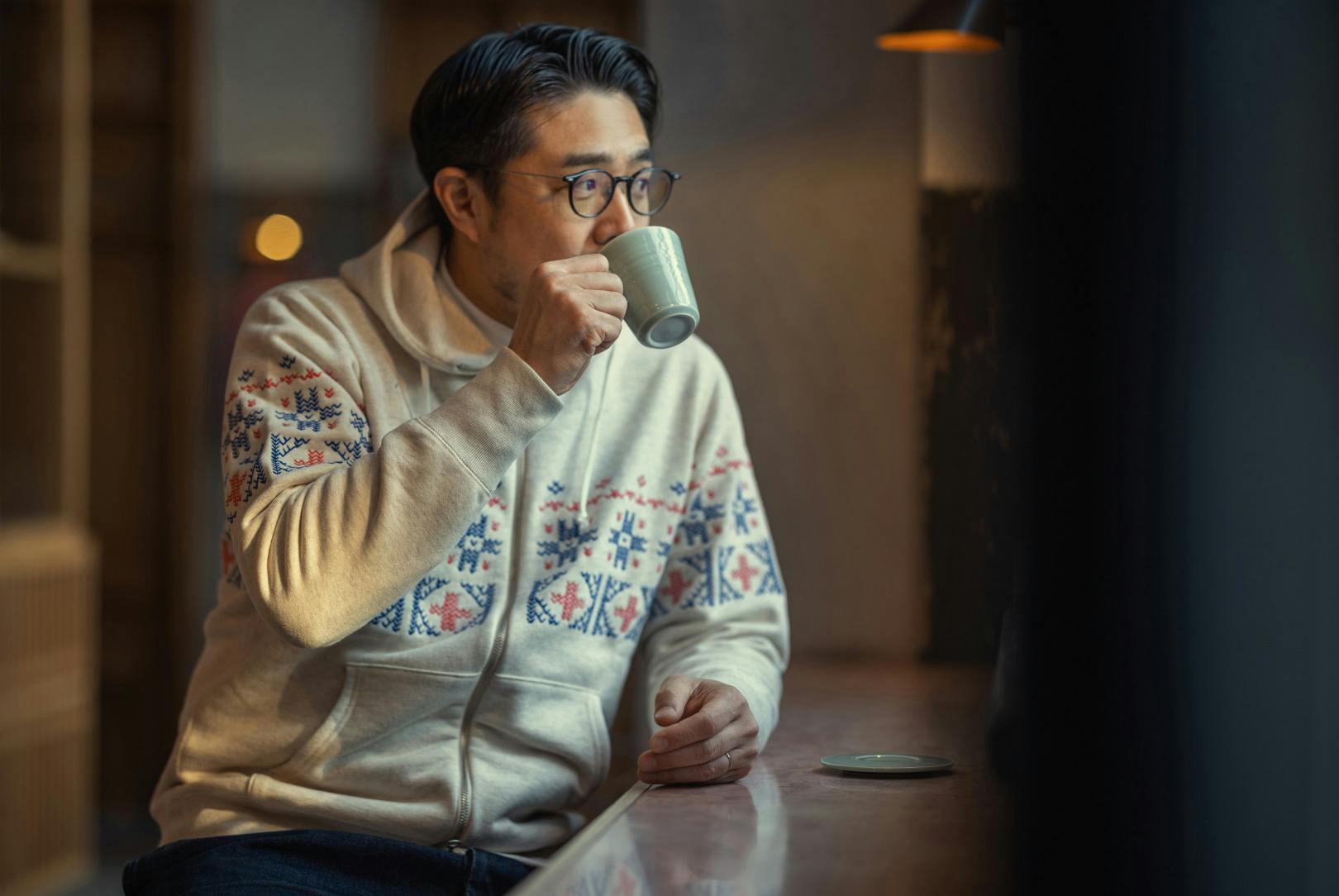
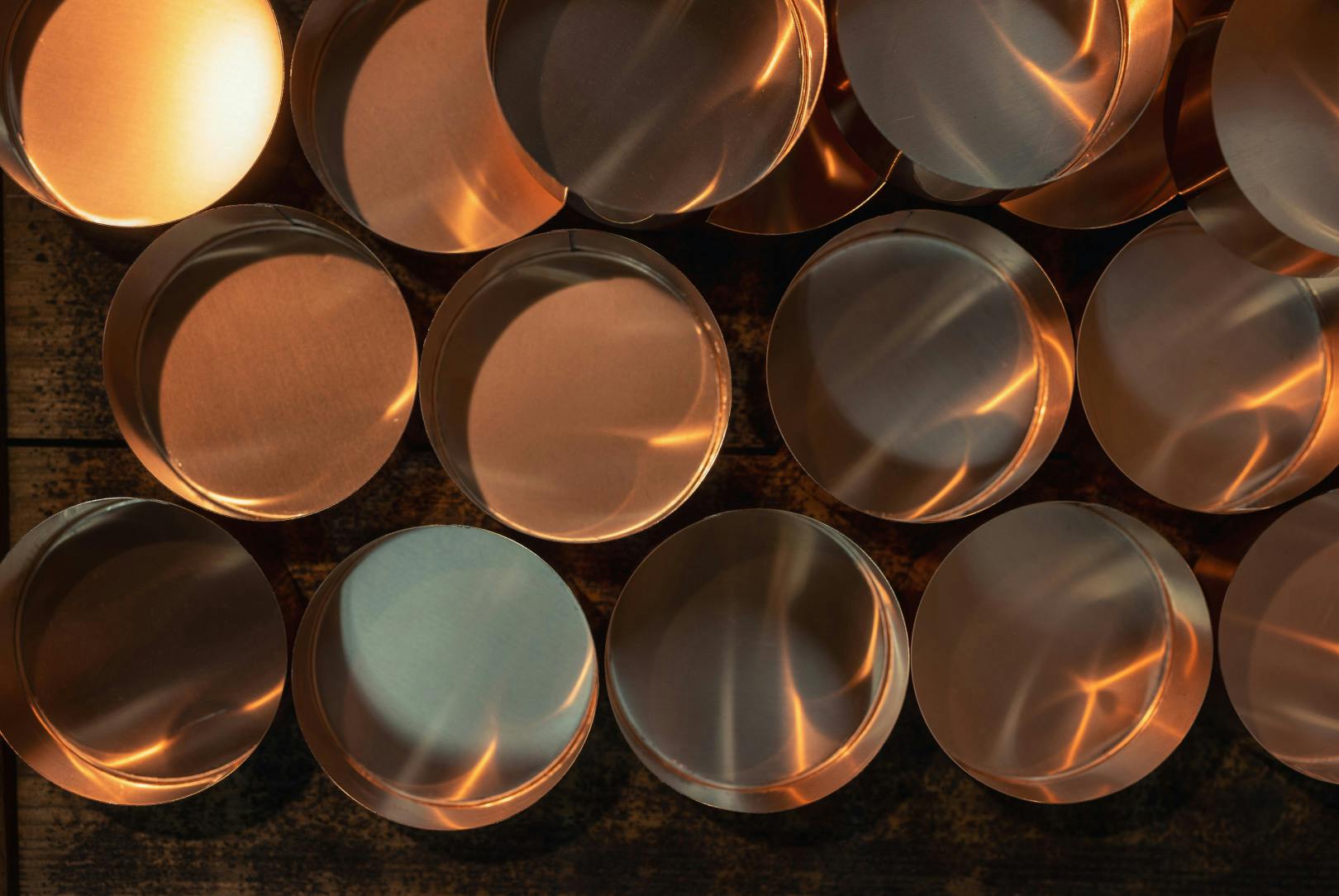
In the front section of the workshop, Seiji completes one of the final steps in the production process. Taking the body of a tea canister in one hand, he searches for a lid with the corresponding number. During the early stages of production, bodies and lids are arranged in pairs, ensuring that at the penultimate stage, they come together as one in the most seamless way possible. Lowering his eyes to canister level, he attaches the lid and watches closely as it descends, expelling the air within until it finally settles. If the lid does not float as desired, he will pause to massage the forms ever so slightly, before repeating the process again. Throughout this routine he intuitively reviews each product, ensuring it meets his high standards.
“When inspecting canisters, I just draw on my experience. I’ve been making them non-stop for more than 50 years, while also interacting with all kinds of customers, so I’ve naturally come to understand what makes a good product. Instead of checking this or that, the essence of Kaikado and our craftsmanship has become clear over time.”
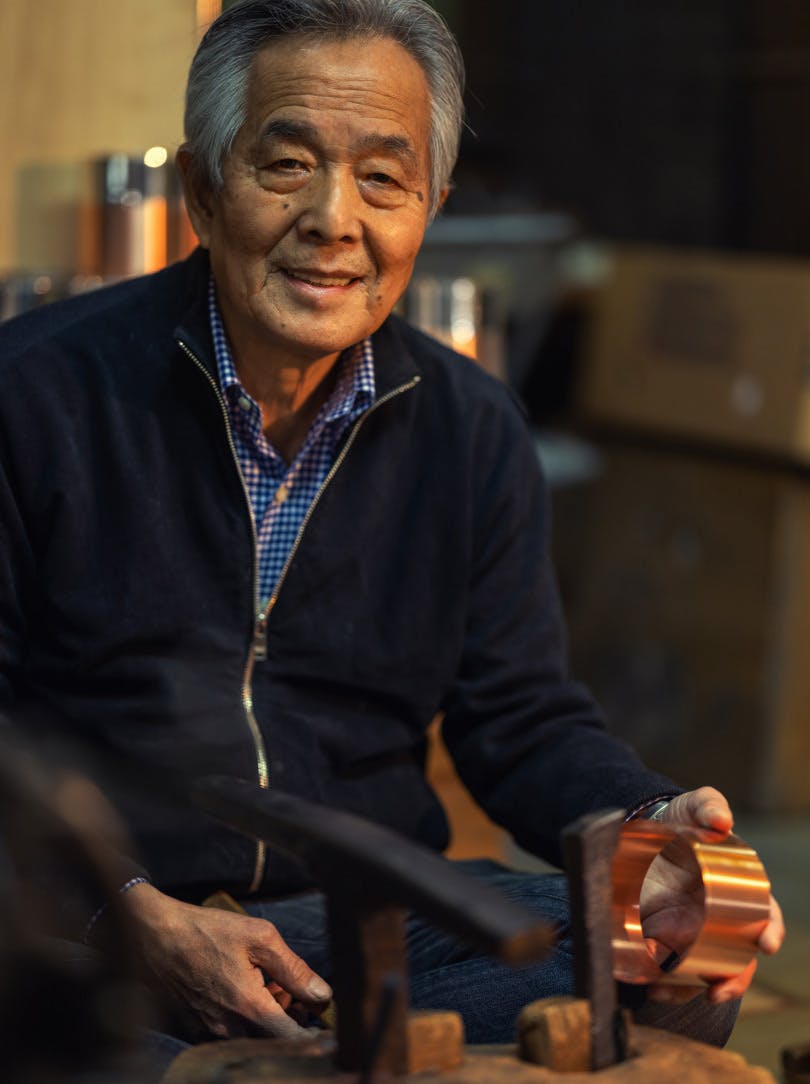
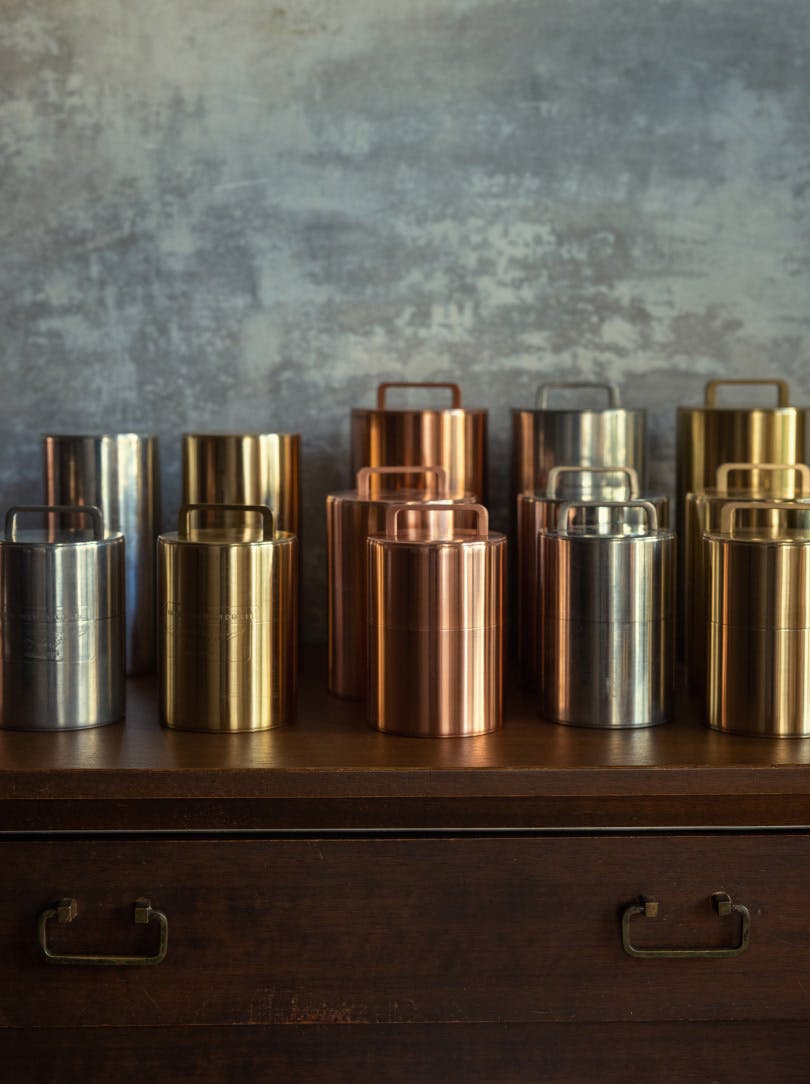
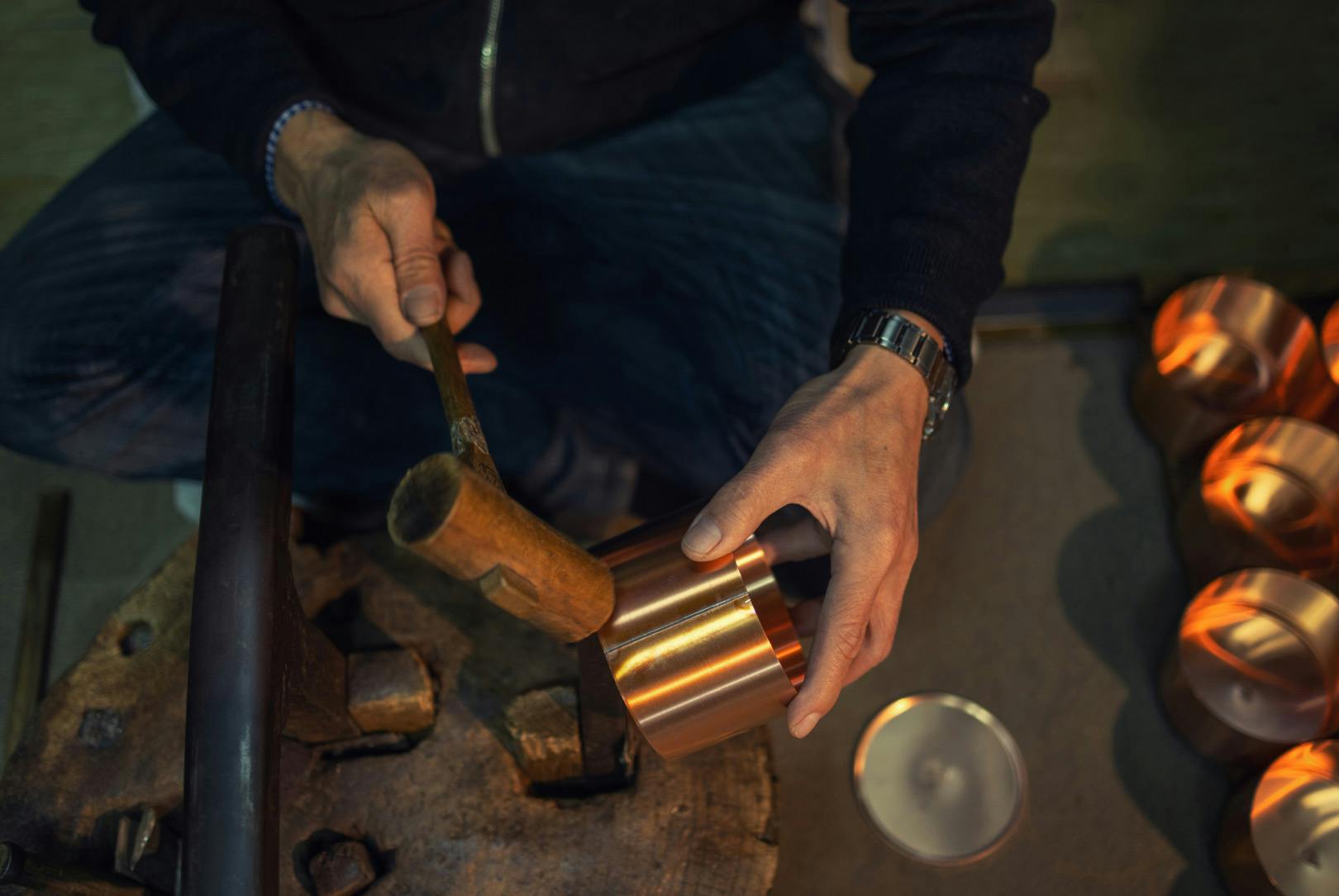
Once the inspection process is complete, the canisters are polished and packaged, before eventually making their way out into the world. And from that point onwards, the living tools are in a constant state of evolution.
“Kaikado’s approach is based on making things that become one with the user,” says Seiji. “Craftspeople don’t make for themselves, they think about how other people will use things they make. Even after we’ve made a canister, it is still not complete. It’s not until it has been used for a long time that it becomes truly complete. Each product ages according to how it’s used, which can vary widely from one person to the next.”
“Brass may become more yellow or pink in colour, depending on what someone eats and the chemical reaction caused by the oils on their hands. Everyone is different, even subtly, and so the canister turns into their own one-of-a-kind item. I think this is a fascinating thing to enjoy,” adds Takahiro. “Things that are beautiful, always looking brand new, aren’t so interesting to me. Instead, I like to think that someone can enjoy using a canister today, imagining what it’ll be like 10, 20 or even 30 years from now.”